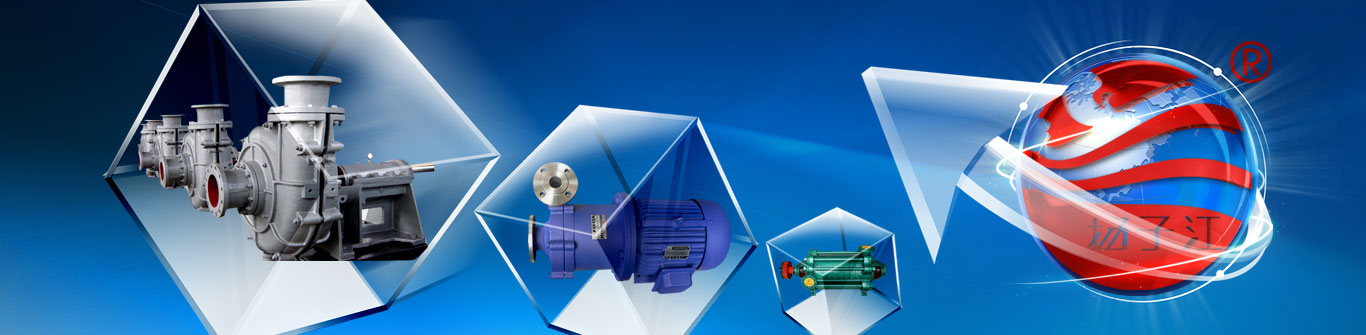
Shield mud delivery control system is a proprietary product developed to control mud delivery of slurry shield machines. The self-contained auto-control system is a network control system composed of a master station (for master control and remote monitoring) and a number of slave stations (for local control), providing for both local and remote control of mud delivery. Flexibly configured, the system allows operation both independent from and in connection with the original system of the slurry shield machine. Each of the slave stations can also work together with the original mud delivery control system of the machine. Communication is possible between the master station and the shield machine either via the related protocol or through physical connection (I/O). Necessary allowances are also provided for interfacing with all types of shield machines easily and freely.
Functions of the master station control system
1. The master station of the control system monitors and remotely operates the mud delivery system of the shield machine. It also remotely monitors and controls the P0 pump, valve block and nozzle cylinder, and provides support to HMI display by interlocking with the host computer of the shield machine.
2. Designed for PLC+HMI, the master stations supports bus communication, providing for a maximum of 32 slave stations and a maximum transmission rate of 12MBit/s. The I/O module receives START/STOP orders from the operation panel and indicates the operating status of the pump.
3. Operation indication panel provides options for operation either from operation panel or through HMI. The HMI working screen displays the current, voltage, speed, pipe flow, the level and pressure of the excavation chamber, and the operating status, failure treatment and auxiliary operations of each of the pumps.
4. The master station acquires on real-time basis the level and pressure of the excavation chamber mounted at the head of the shield machine, with an indicator indicating the percentage of liquid level and a digital meter indicating the pressure.
Slave station control cabinet
1. Smart pump control cabinets and valve control boxes designed for PLC control are mounted next to their respective pumps or valves. To make operation and commissioning easier, each mud pump control system provides for both local and remote control. The control system communicates with the master station via profibus.
2. Slave PLC are responsible for acquiring and processing signals from solenoid valves and pressure sensors on pumps, motor cooling fans, seal water pumps or pipes, or pressure and flow signals of cabinet ventilation and cooling or the mud delivery system; setting, monitoring and controlling their process parameters, and monitoring and controlling the interlocked control, alarm detection and variable-frequency protection of equipment.
3. A display terminal mounted on the control cabinet panel displays parameters of the mud pump in service, such as motor current, motor temperature, motor speed and converter failure information.
4. To avoid attenuation of signal transmission, a photoelectric isolating relay amplifier is incorporated into each of the local control cabinets.